2021-06-29
View Details +CONTACT US
Add: Room 204, Building 1, Zhifu Baili Industrial Park, No. 28 Nanguo West Road, Daliang Street, Shunde District, Foshan City, Guangdong Province, China
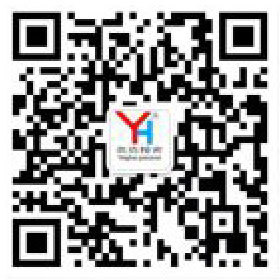
2021-06-29
View Details +Add: Room 204, Building 1, Zhifu Baili Industrial Park, No. 28 Nanguo West Road, Daliang Street, Shunde District, Foshan City, Guangdong Province, China